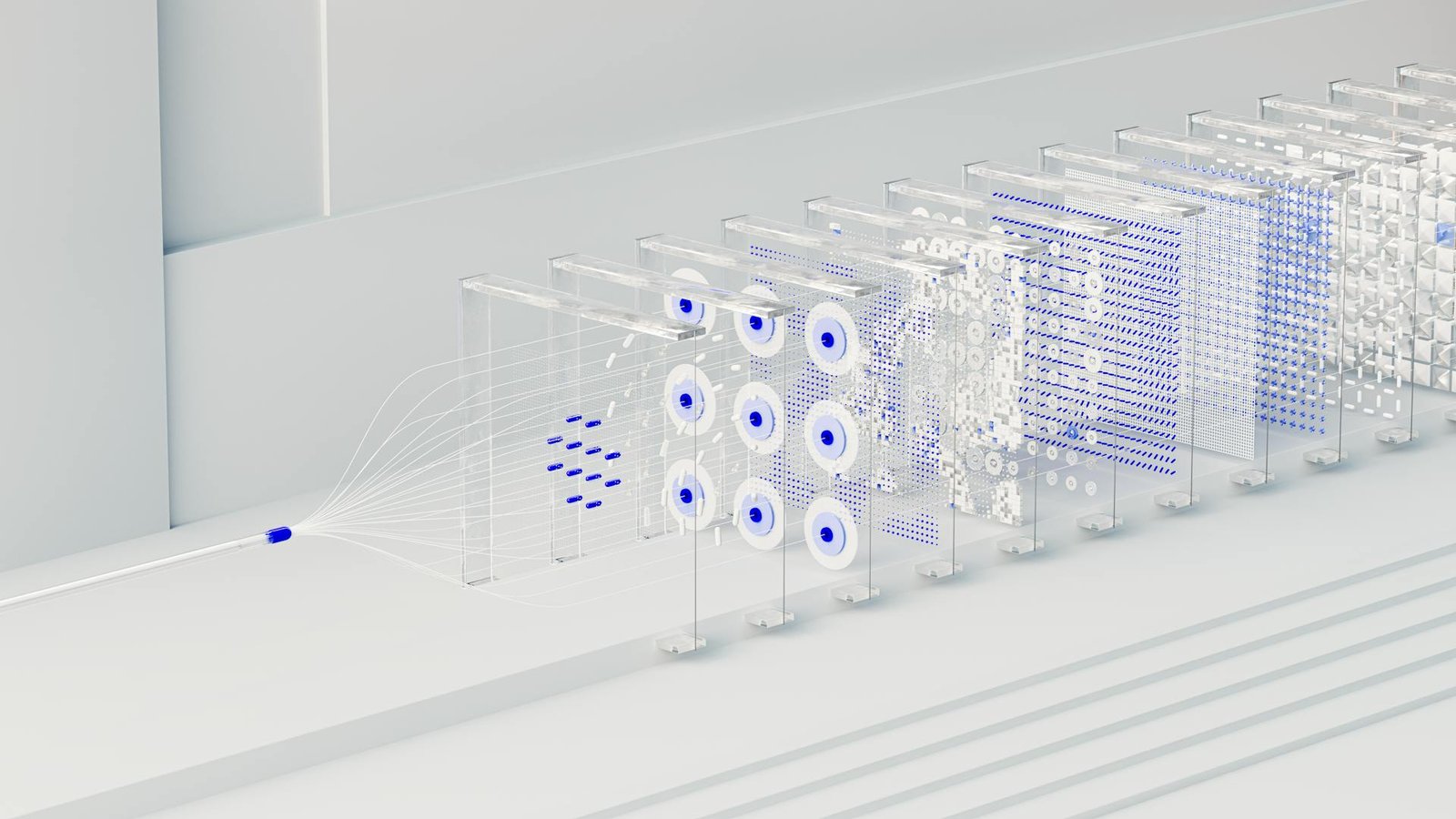
Utilizing Digital Twins for Predictive Maintenance and Optimization
The concept of digital twins has gained significant traction across various industries, from manufacturing and energy to healthcare and logistics. A digital twin is a virtual representation of a physical entity, system, or process that can simulate its real-time performance. By leveraging data from sensors, IoT devices, and advanced analytics, digital twins provide invaluable insights, enabling businesses to optimize operations, enhance decision-making, and improve predictive maintenance.
This article covers the fundamentals of digital twins, their applications, benefits, challenges, and their transformative potential in an industrial context.
Understanding Digital Twins
Definition and Components
A digital twin is essentially a digital replica of a physical object, system, or process. It encompasses three key components:
1. Physical Entity: This is the real-world object, system, or process being represented. It can range from a single machine to an entire production line or even a complete facility.
2. Virtual Model: The virtual counterpart that mirrors the physical entity, often created using computer-aided design (CAD) software and simulation tools. This model is continuously updated with data from the physical entity, enabling real-time monitoring and analysis.
3. Data Connectivity: Sensors and IoT devices collect data from the physical entity and transmit it to the virtual model. This connectivity is crucial for maintaining the accuracy and relevance of the digital twin, allowing it to reflect the real-time state of its physical counterpart.
How Digital Twins Work
Digital twins operate by utilizing data collected from sensors embedded in the physical entity. This data is transmitted to the virtual model, which simulates the entity’s behavior and performance. Advanced analytics and machine learning algorithms can identify patterns, detect anomalies, and predict future performance. The real-time feedback loop enables businesses to make informed decisions, enhancing operational efficiency and driving innovation.
For example, consider a wind turbine equipped with numerous sensors. These sensors monitor parameters such as blade rotation speed, temperature, and vibration. This data is sent to the digital twin, which simulates the turbine’s operational performance. If the digital twin detects abnormal vibrations, it can signal the need for maintenance before a critical failure occurs.
Applications of Digital Twins in Industry
Predictive Maintenance
One of the most significant applications of digital twins is in predictive maintenance. By continuously monitoring the condition of machinery and equipment, digital twins can predict when a machine is likely to fail. This proactive approach allows organizations to perform maintenance before a breakdown occurs, reducing downtime and minimizing repair costs.
In manufacturing, for instance, sensors can monitor the temperature, vibration, and performance of machines. If the digital twin detects an anomaly—such as increased vibration levels—it can alert maintenance personnel to investigate the issue before it leads to a failure. This shift from reactive to proactive maintenance not only enhances operational efficiency but also extends the lifespan of equipment.
Moreover, predictive maintenance contributes to better resource allocation. By understanding when maintenance is likely needed, organizations can schedule repairs during off-peak times, ensuring that production schedules are not disrupted.
Process Optimization
Digital twins enable organizations to optimize processes by simulating various scenarios and identifying the best course of action. By modeling the entire production line or supply chain, companies can analyze factors such as workflow, resource allocation, and production rates. This allows them to make data-driven decisions that enhance efficiency and reduce waste.
For instance, a manufacturing facility can use digital twins to simulate changes in machinery configurations or production schedules. By analyzing the impact of these changes on overall productivity, organizations can identify the most effective strategies for improving throughput.
In logistics, a digital twin can simulate different shipping routes to identify the most efficient paths, taking into account variables such as traffic patterns, weather conditions, and delivery times. This optimization can lead to reduced transportation costs and improved customer satisfaction.
Product Development and Testing
Digital twins also play a crucial role in product development and testing. By creating virtual models of new products, organizations can simulate performance, conduct stress tests, and identify potential design flaws before physical prototypes are built. This approach accelerates the product development cycle and reduces the costs associated with physical testing.
In the automotive industry, manufacturers can use digital twins to model vehicle performance under various driving conditions. By simulating crashes, handling, and environmental factors, companies can refine their designs and ensure safety standards are met before launching a new vehicle.
Furthermore, digital twins allow for rapid prototyping. If a design change is required, engineers can adjust the virtual model and immediately see the potential impact on performance. This iterative process leads to more innovative products that better meet customer needs.
Training and Simulation
Digital twins can serve as powerful training tools for employees. By creating a virtual replica of a work environment, organizations can conduct training simulations that mirror real-world scenarios. This allows employees to gain hands-on experience without the risks associated with operating real machinery or working in hazardous environments.
For example, in the oil and gas industry, digital twins can simulate drilling operations, allowing operators to practice and refine their skills in a controlled environment. This not only enhances employee readiness but also contributes to safety and efficiency in real-world operations. Employees can encounter various scenarios—such as equipment failures or emergency situations—within the simulation, preparing them for real-life challenges.
Moreover, digital twins can be used for onboarding new employees, providing them with immersive experiences that familiarize them with equipment and processes before they step onto the shop floor.
Supply Chain Management
Digital twins can revolutionize supply chain management by providing a comprehensive view of operations. By creating a virtual representation of the entire supply chain, organizations can monitor inventory levels, track shipments, and identify bottlenecks in real-time.
This holistic view allows for better decision-making and resource allocation. For instance, if a supplier is delayed, the digital twin can model alternative sourcing strategies or adjust production schedules to minimize disruptions. By simulating various scenarios, businesses can respond swiftly to changes in demand or supply, maintaining operational continuity.
Furthermore, digital twins can enhance collaboration between different stakeholders in the supply chain. With a shared virtual model, all parties can access real-time data, leading to improved communication and coordination.
Benefits of Digital Twins
Improved Decision-Making
By providing real-time insights and predictive analytics, digital twins empower organizations to make informed decisions. With access to accurate data, leaders can identify potential issues, assess risks, and allocate resources more effectively. This leads to more strategic planning and resource management, ultimately enhancing the organization’s overall performance.
Enhanced Efficiency
Digital twins streamline operations by optimizing processes and reducing downtime. Predictive maintenance minimizes unexpected failures, while process optimization leads to more efficient workflows and reduced resource consumption. For instance, by leveraging digital twins, a manufacturing facility may achieve a significant reduction in production cycle times, leading to increased output and revenue.
Cost Savings
By implementing digital twins, organizations can significantly reduce maintenance costs, minimize downtime, and improve resource allocation. The proactive nature of predictive maintenance translates into fewer emergency repairs and extended equipment lifespans, resulting in substantial savings over time. Additionally, the insights gained from digital twins can lead to more informed purchasing decisions, reducing unnecessary expenditures on materials and supplies.
Increased Agility
Digital twins enable organizations to quickly adapt to changes in demand, market conditions, or operational challenges. By simulating various scenarios, businesses can assess potential impacts and pivot their strategies accordingly, fostering greater resilience in a rapidly evolving landscape. This agility is particularly valuable in industries facing frequent disruptions, such as retail and logistics.
Enhanced Customer Experience
With the insights gained from digital twins, organizations can tailor their offerings to meet customer needs more effectively. By understanding how products are used in real-time, companies can make informed decisions about enhancements or modifications, ultimately improving customer satisfaction and loyalty.
Challenges in Implementing Digital Twins
Data Management and Integration
Creating and maintaining digital twins requires a substantial amount of data from various sources. Organizations must ensure that data is accurate, timely, and integrated seamlessly into the digital twin. This can be a significant challenge, particularly for companies with legacy systems or disparate data sources. Achieving a unified view of data can require significant investments in IT infrastructure and analytics capabilities.
Cybersecurity Risks
The increased connectivity associated with digital twins raises concerns about cybersecurity. As organizations collect and transmit data, they become more vulnerable to cyberattacks. Protecting sensitive data and ensuring the integrity of digital twins is paramount to mitigate risks. This requires robust cybersecurity protocols, regular audits, and employee training to recognize potential threats.
Cost of Implementation
Implementing digital twin technology can be a costly endeavor, requiring investment in IoT devices, data analytics tools, and skilled personnel. Smaller organizations may find it challenging to allocate resources for this transformation. However, the long-term benefits often outweigh the initial costs, making it a worthwhile investment. To minimize costs, organizations can consider phased implementations or pilot projects that allow for gradual integration.
Skill Gaps
The successful implementation of digital twins requires a skilled workforce that understands both the technology and the specific industry. Organizations may face challenges in finding qualified personnel or upskilling existing employees, which can impede the adoption of digital twin technology. Investing in employee training and development is essential to build the necessary skills for operating and maintaining digital twin systems.
Future of Digital Twins in Industry
The future of digital twins is promising, with advancements in AI, machine learning, and IoT set to enhance their capabilities further. As industries continue to embrace Industry 4.0 principles, digital twins will play a pivotal role in driving innovation and operational excellence.
Integration with AI and Machine Learning
Emerging technologies such as artificial intelligence and machine learning will further enhance the capabilities of digital twins. By leveraging AI algorithms, organizations can gain deeper insights from their digital twins, enabling more accurate predictions and better decision-making. Machine learning can continuously improve the digital twin’s accuracy by learning from new data, allowing organizations to adapt to changing conditions more effectively.
Enhanced Collaboration with Augmented Reality (AR)
The integration of augmented reality (AR) with digital twins offers exciting possibilities for training, maintenance, and remote support. AR can overlay digital twin data onto the physical world, providing real-time insights to technicians during maintenance tasks. This allows for more efficient troubleshooting and repair processes, reducing downtime and improving service quality.
Sustainability and Environmental Impact
As sustainability becomes a critical focus for organizations, digital twins can assist in optimizing energy consumption, reducing waste, and improving resource management. By simulating the environmental impact of various operational scenarios, businesses can make more sustainable choices. For instance, digital twins can help organizations model the effects of energy-saving measures, enabling them to evaluate the potential benefits before implementation.
Continued Evolution of Smart Factories
Digital twins are integral to the development of smart factories, where interconnected machines, systems, and processes work in harmony. As the Internet of Things (IoT) continues to expand, the number of data points available for digital twins will increase, allowing for more sophisticated models. This evolution will lead to even greater efficiencies and enhanced productivity in manufacturing and other sectors.
Conclusion
Digital twins represent a transformative technology that is reshaping industries by providing real-time insights, enhancing predictive maintenance, and optimizing processes. By creating virtual replicas of physical entities, organizations can make data-driven decisions that improve efficiency, reduce costs, and foster innovation.
While challenges such as data management, cybersecurity, and implementation costs exist, the benefits of digital twins far outweigh these obstacles. As industries continue to evolve and adopt advanced technologies, digital twins will play an increasingly crucial role in driving operational excellence and enhancing competitiveness.
In a world where data and technology are integral to success, embracing digital twin technology can position organizations at the forefront of their industries, enabling them to navigate complexities and seize new opportunities. The future is bright for digital twins, and their potential to revolutionize industrial practices is just beginning to be realized. As companies continue to invest in and explore this technology, the possibilities for innovation, efficiency, and sustainability will only expand, promising a new era of operational excellence.